
Our Story
More than 30 years have passed since we first applied
our Knowledge & Engineering Experience in Design & Manufacturing of Steel Based Products, Providing Solutions for CNC Robotic in Manufacturing Automation Environment.
We have since, Constantly Evolved to Provide Various Engineered Solutions using Advanced Composites and 3D Automation.

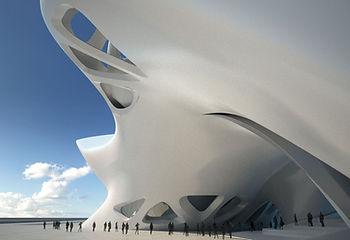
With the global pursuit and implementation of carbon reduction, we anticipate a transformative shift in the market dynamics of steel and aluminium-based products.
This transformation relies on manufacturers' unique ability to reduce CO2 emissions, evaluated through thorough cradle-to-gate Life Cycle Analysis (LCA).
Incorporating advanced composite products and technology, is now a crucial strategy, offering benefits such as improved structural efficiency, decreased weight, and enhanced durability.
These factors collectively contribute to a significant reduction in the carbon footprint across the entire product life cycle.
When clients started conceptualizing increasingly sophisticated architectural products, the constraints of carbon steel became evident. Several years ago, our engineers seized the opportunity to offer manufacturing solutions for distinctive decorative light poles showcased on the left. Subsequently, steel products began undergoing transformative changes, driven by a growing appetite for imaginative and dynamic designs demanded by architects, engineers, and designers. Their creativity in seeking engineered art solutions became more daring. However, the manufacturing sector lagged behind, struggling to fabricate these innovative design concepts with effectiveness, safety, and efficiency.
As architects, engineers, and designers are exploring more organic structures while ensuring strict compliance, the demand is pushing traditional materials like carbon steel to their limits.
In response to this challenge, we have harnessed the advantage of advanced composites, integrating them with state-of-the-art 3D machinery and innovative mold production processes. The synergy of these technologies has yielded groundbreaking solutions, catering to the demands of a new and eager era in 3D fluid organic architecture scenes.
This convergence of cutting-edge materials and manufacturing techniques not only meets but exceeds the expectations of the industry, providing a transformative shift in the possibilities for creative and structurally sound architectural designed products.
SIFT CENTER offers solutions to bridge the gap between cutting-edge concept designs and the manufacturing industry. Our focus is on facilitating the transition towards more organic and fluid structural solutions, employing advanced composites.
SIFT CENTER adeptly addresses this gap by swiftly identifying the production challenges associated with new design concepts. Our engineers specialize in tailoring unique solutions to overcome these limitations. With in-house expertise in developing CNC machinery, automation processes, and a profound understanding of composite plug and mold production, we are well-equipped to deliver rapid solutions for the composite industry. Whether it's in architecture, automotive, rail, marine, or industrial products, we confidently provide quick turnaround solutions.
In conjunction with our in-house engineering machinery and process solutions, SIFT CENTER collaborates closely with key global partners from advanced material producers. This collaborative effort enables us to tailor custom-engineered solutions that align seamlessly with our clients' objectives and expectations.
As architects and engineers increasingly seek bolder solutions in their designs, exemplified by the depicted concept on the left, with award-winning designs by Zaha Hadid Architects, SIFT CENTER eagerly anticipates offering the necessary engineering support, facilities, and manufacturing solutions to bring these visionary designs to reality.
We invite you to contact us for your requirements!